Fabrication Processes
We provide diverse metal fabrication processes, from traditional techniques to advanced 3D printing, meeting all your needs:
Powder metallurgy
Metal injection molding
Metal powder press sintering
Ceramic injection molding
3D Printing
SLM (Selective Laser Melting)
LSF (Laser Solid Forming)
LC (Laser Cladding)
Magnet Fabrication
NdFeB, SmCo, AlNiCo, Ferrite
Casting (Die casting, Investment casting, Sand mold casting)
Materials
We use a wide range of metal materials and alloys to meet different application requirements:
Aluminum alloyStainless steelMagnesium alloyTitanium alloyZinc alloyCopper baseIron-basedNickel alloyPlasticMagnetsFabrication Process
【STEP 1:Consultation & Discussion】
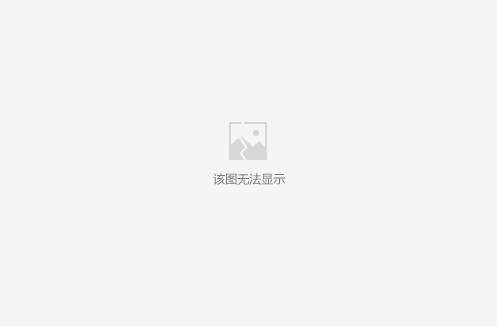
Before project initiation, we require detailed drawings and parameters to provide accurate quotations and optimal fabrication solutions:
Drawing Requirements
3D Drawings: igs, step, prt, x_t, sldprt, mcam, mcx, stl
2D Drawings: dwg, dxf, pdf, jpg, etc.
Quotation Parameters
Materials, surface treatment, hardness requirements, or other mechanical properties
Aesthetic requirements, quantity, etc.
Contact information: Company name, contact person, phone number, and address
Process Confirmation
We select the best process based on part structure, material, and cost-effectiveness:
Complex structures: Prioritize MIM or 3D printing
Different materials: e.g., MIM for stainless steel, casting for aluminum alloy
Cost consideration: Low-cost processes for parts with general performance requirements
【STEP 2:APQP】
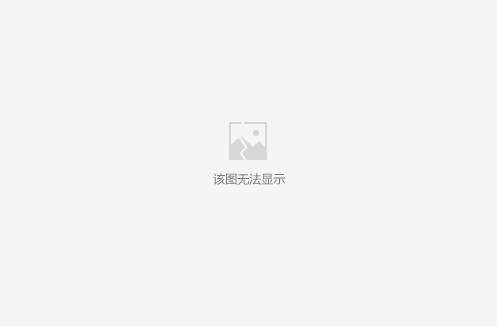
Pre-Molding Preparation
Raw material preparation: Prepare materials according to customer drawings and conduct 100% raw material inspection
Mold design and processing: Professional mold engineers design molds using CNC, EDM, and other processes
Sample Production
Strictly follow internal standard operating procedures, optimize processes based on customer standards and actual dimensions, and document all processes in standard APQP files (control plan, FMEA, etc.).
Post-Processing
Heat treatment: Enhance part surface hardness and performance
Surface treatment: Electroplating, PVD, polishing, etc., to improve surface finish and corrosion resistance
Product inspection: Check appearance, dimensions, and performance to ensure no defective products are delivered
【STEP 3:LONG TERM COOPERATION】
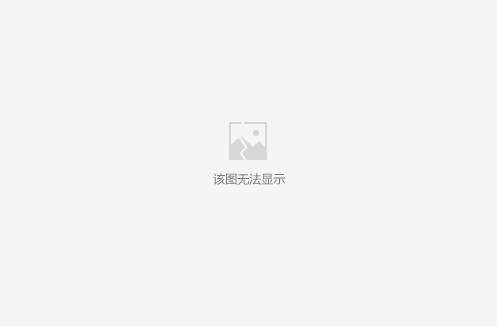
Mass Production
Customized customer files for each client, mass production of mature products following approved sample processes, with a 99.8% on-time delivery rate. Quality department conducts continuous inspections during production.
Packaging and Shipping
Professional tooling masters select reasonable customized packaging solutions based on product characteristics to prevent damage during transportation.
Feedback
Quick response within 2 hours to customer quality feedback, with a dedicated team initiated for 8D problem-solving processes. 100% satisfaction guarantee for after-sales issue resolution.
Do You Know What Factors Affect Processing Costs?
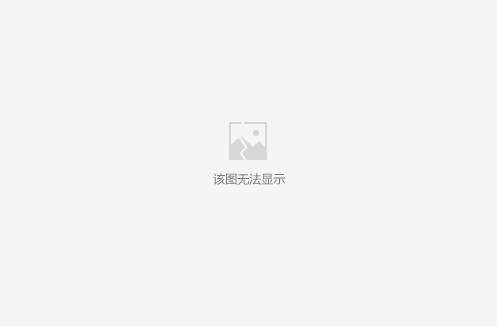
The price of metal parts depends on the following factors:
Processing Time - Longer machining time increases costs, especially for CNC machining
Shapes and Structures - Multi-curved products require 4-axis/5-axis machining; dense ribs and internal right angles increase processing costs
Materials and Surface Treatment - Material cost varies significantly; special surface treatments require higher raw material quality
Custom Tooling - Angled holes require special fixtures or index plates
How to Optimize Design to Reduce Processing Costs
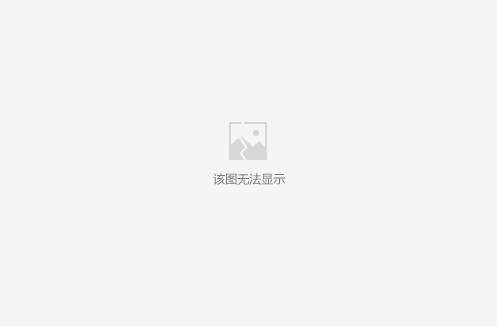
Consider the following design optimizations to reduce costs:
Change internal right angles to radii (R angles)
Reduce the number of ribs
Increase wall thickness
Use standard hole diameters or threads whenever possible
Select appropriate materials and surface treatments
Specify only necessary and critical tolerances
For more professional high-value advice, contact our technical team.